現代の製造業界は、グローバル競争の激化や顧客ニーズの多様化により、高い生産性と品質が求められています。本記事では、製造業における作業効率を効果的に向上させるための具体的な方法やツールの活用法を解説します。
これらの手法を取り入れることで、生産性向上とコスト削減を実現し、競争力強化につなげることができるでしょう。
製造業における作業効率を上げる方法
製造業の作業効率向上には、データ活用と業務プロセスの最適化が不可欠です。まずは現状の課題を把握し、改善ポイントを明確にしましょう。
生産効率とは?基本概念の解説
生産効率とは、投入したリソース(人員、時間、原材料など)に対して得られる生産量の比率のことです。これを高めるには、同じリソースでより多くの生産を行うか、同じ生産量をより少ないリソースで達成する必要があります。効率向上の第一歩は、生産量、作業時間、材料使用量などのデータを継続的に収集・分析し、現状を「見える化」することから始まります。
なぜ製造業の効率化が必要なのか?理由と背景
製造業の効率化が求められる背景には、人手不足の深刻化、原材料価格の上昇、国際競争の激化などがあります。特に少子高齢化による労働人口の減少が進み、製造現場の人材確保が困難になっています。
また、顧客ニーズの多様化により多品種少量生産へのシフトが進み、従来の大量生産モデルでは対応しきれなくなっているケースも増えています。効率化は単なるコスト削減だけでなく、変化する市場環境への適応力を高める不可欠な取り組みです。
データ活用による業務改善の具体的手法
製造現場から収集したデータを活用することで、生産性のボトルネックを特定し、品質不良の原因を究明できます。まずは適切なKPI(重要業績評価指標)を設定し、定期的に測定・評価する仕組みを構築しましょう。データに基づいた意思決定により、主観や経験だけに頼らない効果的な改善活動が推進できます。
効果的な効率化ツールの導入
製造業の効率化を推進するためには、適切なツールの導入が不可欠です。目的に合ったシステムやテクノロジーを選び、現場に適応させることが重要です。
生産管理システムの選び方と活用法
生産管理システムを導入する際は、自社の業務フローと合致したものを選ぶことが重要です。必要な機能(生産計画、在庫管理、工程管理など)を明確にし、既存システムとの連携性も考慮しましょう。
販売管理や会計システムとスムーズに連携できるシステムを選ぶことで、データの二重入力を防ぎ、情報の一元管理が実現します。導入後は、現場スタッフへの教育を丁寧に行い、実際の運用状況を定期的に確認・改善することが成功の鍵です。
IoTを使ったリアルタイムのデータ収集と分析
IoT技術を活用することで、製造設備の稼働状況や環境データをリアルタイムで収集・分析できます。センサーを製造ラインに設置し、常時監視することで、異常の早期発見や予防保全が可能になります。
収集したデータはクラウド上で統合・分析され、ダッシュボードを通じて視覚的に確認できます。異常値が検出された場合は自動的にアラートを発信するシステムにより、トラブルの早期対応が可能になり、ダウンタイムを削減できます。
自動化による作業時間の短縮と品質向上
自動化技術の導入は、作業時間の短縮と品質の安定化に大きく寄与します。単純作業や繰り返し作業は自動化し、人間はより付加価値の高い業務に集中できる環境を整えましょう。
産業用ロボットやコボット(協働ロボット)の導入は、人手不足の解消だけでなく、24時間稼働による生産性向上、作業者の負担軽減にもつながります。
自動検査システムにより、人間による目視検査よりも高精度で安定した品質管理が実現します。投資対効果を慎重に検討し、段階的に導入していくアプローチが効果的です。
業務プロセスの見える化による改善
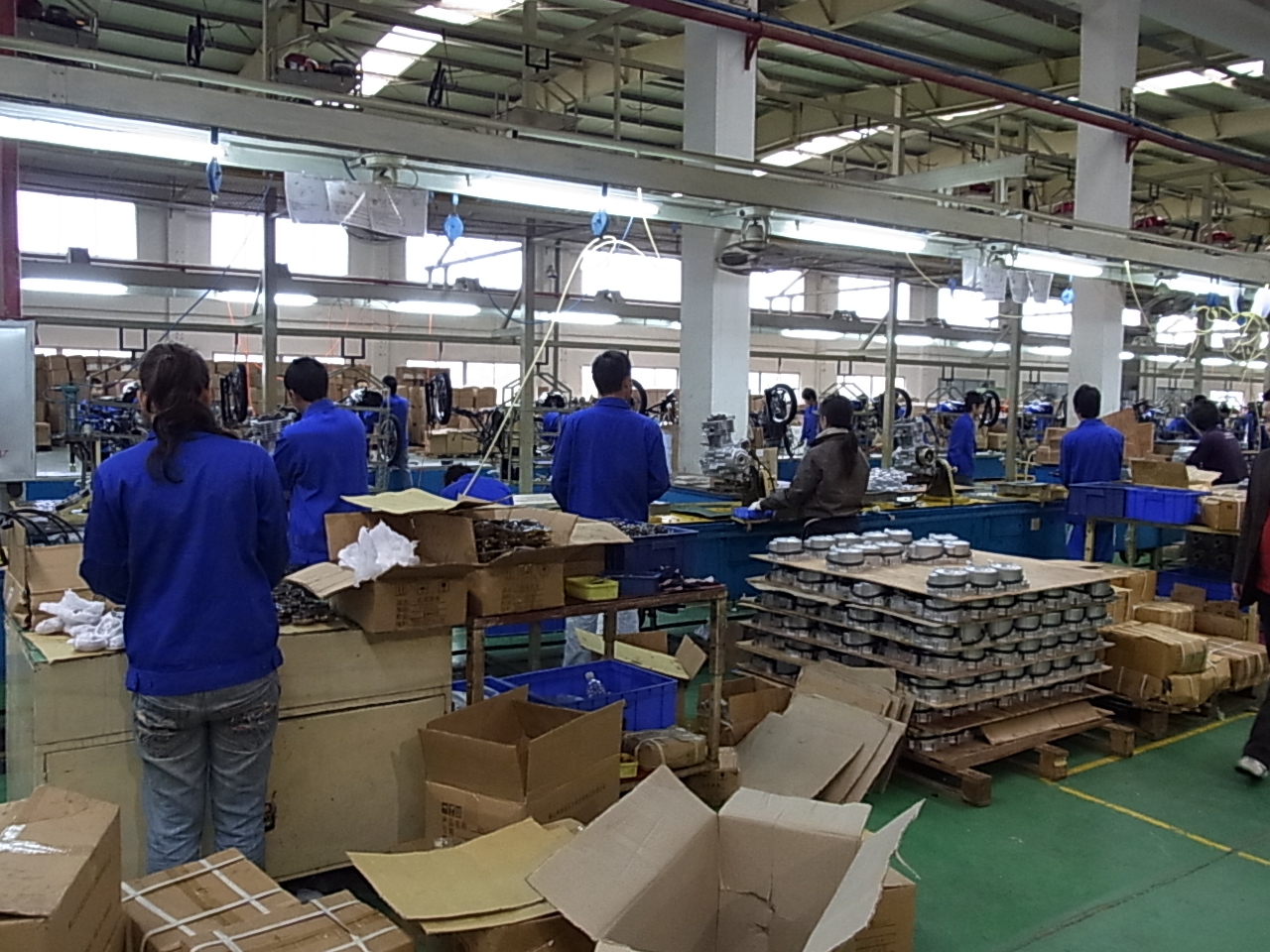
5S活動を通じたムダの排除
5S(整理・整頓・清掃・清潔・躾)は、製造現場の基本的な改善活動です。不要なものを取り除き、必要なものを使いやすく配置し、職場を清潔に保つことで、作業効率の向上と不良品の削減が実現します。
特別な設備投資なしで始められるため、改善文化の醸成にも役立ちます。定期的な巡回チェックや写真による改善前後の比較など、継続的に活動を評価・改善する仕組みを取り入れることが成功の秘訣です。
標準化の進め方と成功事例
作業の標準化は、品質のばらつきを抑え、効率を向上させる重要な取り組みです。最も効率的な作業方法を特定し、誰でも同じように実施できるよう手順書やチェックリストを整備しましょう。
ある自動車部品メーカーでは、作業手順を動画で記録し、タブレット端末で閲覧できるようにしたことで、新人教育の時間が短縮され、熟練作業者の技能伝承もスムーズに行えるようになりました。標準化は一度完成したら終わりではなく、現場からのフィードバックを反映して継続的に改善していくことが重要です。
現場の意見を活かした改善ネタの収集
効果的な改善を進めるには、現場の作業者の声を積極的に取り入れることが重要です。日々の作業で感じる不便さや気づきは、貴重な改善のヒントとなります。
提案制度や改善ボードの設置など、意見を出しやすい仕組みを整え、定期的な改善ミーティングで現場の声を直接聞く機会を設けることも効果的です。提案を実現した際は、その効果を見える形で共有し、提案者を適切に評価することで、継続的な改善文化が醸成されます。
生産性向上のためのレイアウト見直し
効率的な生産ラインの設計とは
効率的な生産ラインは、製品の流れがスムーズで、工程間の滞留が最小限になるように設計されています。製品の特性や生産量に応じて、直線型、U字型、セル生産型などの適切なレイアウトを選択します。
多品種少量生産ではセル生産方式が効果的なことが多く、大量生産では直線型のラインが適しています。将来の生産量の変動や製品の変更にも柔軟に対応できるよう、可動式の設備や簡単に組み替えられるラインの構築も検討すべきです。
作業動線の最適化についての考え方
作業者や材料が移動する経路である作業動線を最適化することで、無駄な移動時間を削減し、生産性を向上させることができます。まず現状の移動経路と距離を測定し、図面上に可視化します。
頻繁に使用する設備や工具は作業者の近くに配置し、関連する工程は近接させるなど、移動距離を最小化する工夫が必要です。材料の供給方法や完成品の搬出経路も含めて総合的に検討することで、工場全体の効率化が図れます。
人手不足に対応する設備配置の工夫
人手不足に対応するには、少人数でも効率よく作業できる設備配置が重要です。一人の作業者が複数の機械を担当できるような配置や、移動距離を最小限に抑えたレイアウトを検討しましょう。
自動搬送装置や中間バッファの適切な配置により、作業者の負担を軽減しつつ、生産性を維持することが可能です。また、高齢者や女性でも無理なく作業できるよう、人間工学に基づいた作業高さの調整や補助装置の導入も検討すべきです。
手作業からの脱却と省人化の推進
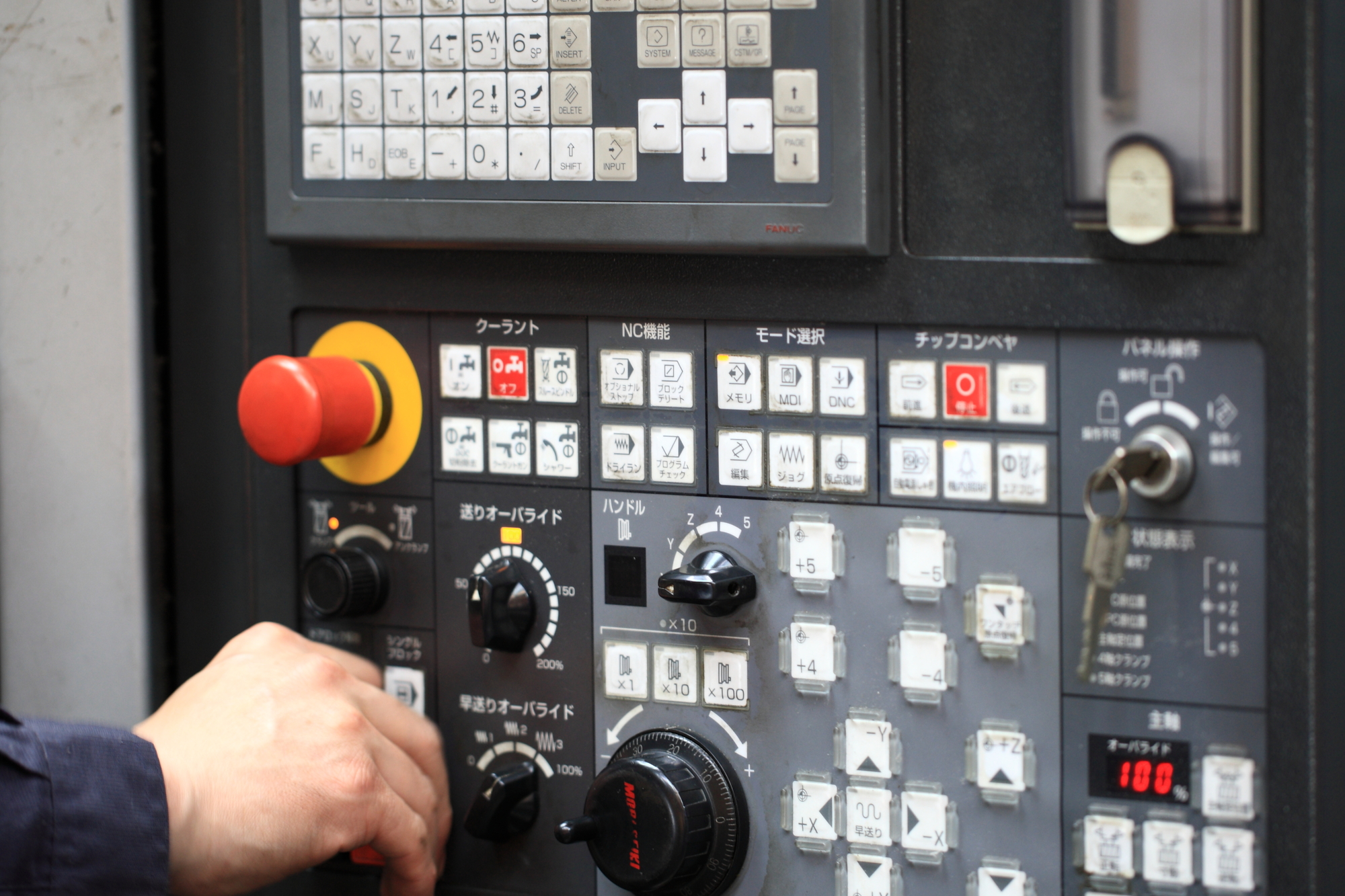
労働生産性を向上させるための設備導入
労働生産性向上には、作業を補助または代替する設備の導入が効果的です。現状の作業分析を行い、人的負担が大きい工程や単純反復作業を優先的に自動化しましょう。初期投資コストだけでなく、保守費用や教育コストも含めた総合的な投資対効果を検討し、段階的な導入計画を立てることが重要です。
ロボット技術を活用した業務の効率化
産業用ロボットやコボットの導入は、人手不足解消と品質安定化に貢献します。特にコボットは安全柵なしで人との協働作業が可能なため、既存ラインへの導入がしやすい特徴があります。
ピッキング、パレタイズ、組立、検査などの作業に適しており、視覚センサーやAIを活用した複雑な作業も可能になってきています。導入後は、運用データを収集・分析し、継続的な改善を行うことで、さらなる効率化が実現できます。
人材不足に対応するためのスキルアップ法
自動化が進んでも、それを運用・保守する人材の育成は不可欠です。OJTと研修を組み合わせたプログラムの構築や、熟練技能者のノウハウをデジタル化して共有する取り組みが重要です。
作業手順の動画マニュアル化やAR(拡張現実)を活用した遠隔指導など、デジタル技術を活用した教育方法も取り入れるべきでしょう。多能工化を進め、少ない人員でも柔軟に対応できる体制づくりも人材不足対策として有効です。
業務改善の成功事例から学ぶ
実際の製造業での効率化の取り組み事例
ある電子部品メーカーでは、生産ラインにIoTセンサーを設置し、稼働率の低い工程を特定・改善したことで全体の生産性が向上しました。食品加工業では、作業者の動作分析を行い、無駄な動きを削減するとともに、作業台や工具の配置を最適化することで生産性が上がりました。
自動車部品メーカーでは、AIを活用した画像検査システムを導入し、検査精度の向上と検査員の負担軽減を同時に実現しています。これらの事例に共通するのは、現状の詳細な分析に基づく改善と、適切な技術の活用です。
成功事例に見る具体的なアプローチ
成功企業の多くは、「小さな成功の積み重ね」を重視し、一気に全工程を改革するのではなく、モデルラインや特定の工程から改善を始め、成功体験を組織内に広げています。
また、トップダウンの改革とボトムアップの改善活動を両立させ、経営層の明確なビジョンと支援のもと、現場の創意工夫を活かす仕組みを整備しています。データに基づく客観的な分析と、現場の経験・知恵を融合させる姿勢が成功の鍵です。
顧客満足度向上のための業務改善の成果
効率化は単なるコスト削減ではなく、顧客満足度の向上にもつながります。ある金属加工メーカーでは、受注から出荷までの業務プロセスを見直し、不要な待ち時間を削減してリードタイムを大幅に短縮したことで、急ぎの注文にも対応できるようになり、新規顧客の獲得につながりました。
品質管理体制の強化により不良品の流出が減少し、クレーム対応コストの削減と顧客信頼の向上を実現した企業もあります。顧客視点での価値向上を念頭に置いた改善活動が、持続的な競争力につながります。
生産におけるミスの原因と対策
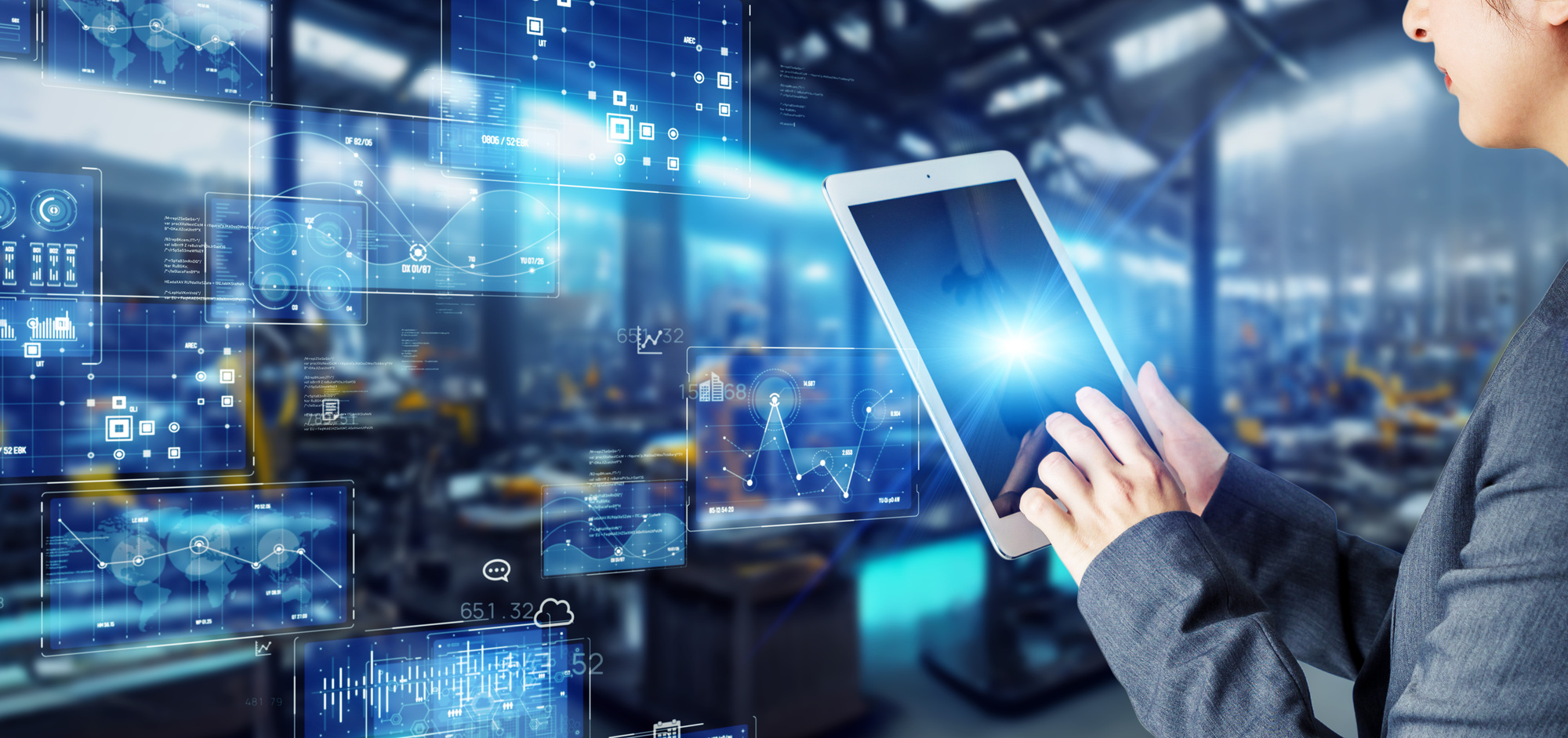
よくあるミスの種類とその影響
製造現場でよく見られるミスには、作業手順の誤り、部品の取り付け忘れ、検査漏れ、設備の誤操作などがあります。これらは不良品発生による手戻りやクレーム対応コストの増加、納期遅延による信用低下など様々な悪影響をもたらします。
特に出荷後に発見される品質不良は、顧客先での不具合として現れ、信頼関係の毀損や風評被害につながる可能性があります。重点的に対策を講じるべき箇所を特定することが重要です。
ミス削減のための教育と管理の方法
標準作業手順書の整備と徹底した教育により、作業者のスキルのばらつきを最小化しましょう。重要工程ではダブルチェック体制を導入するなど、ミスを発見するための仕組みも重要です。
視覚的な作業指示(ビジュアルマニュアル)やポカヨケ(誤り防止装置)の導入も効果的です。ミスが発生しやすい状況(疲労時や急ぎの作業など)を特定し、作業環境や作業配分の見直しで予防することも検討すべきです。
失敗から学ぶ、改善への取り組み
ミスや失敗は改善のための貴重な機会ととらえ、表面的な対応だけでなく根本原因の追究(なぜなぜ分析)を行い、再発防止策を講じましょう。失敗事例を組織内で共有し、類似工程での予防にも活かすことが重要です。
ミスを責める文化ではなく、改善につなげる前向きな風土づくりを心がけ、「失敗は成功の母」という考え方を組織に浸透させることで、継続的な改善が実現できます。
業務効率化に向けた法人連携の重要性
製造業の効率化には、社内各部門や取引先との連携強化が不可欠です。製造部門だけでなく、営業、設計、購買、物流など関連部門との協力により、受注から納品までの全プロセスの効率化が可能になります。
設計部門と製造部門が開発初期段階から協働することで、製造しやすい設計(DFM: Design for Manufacturing)が実現し、生産効率が向上します。サプライヤーとの情報共有も調達リードタイムの短縮や在庫の適正化に重要です。
他部門との連携を強化するためのステップ
部門間連携を強化するには、目標の共有と相互理解が重要です。定期的なクロスファンクショナルミーティングや部門間ローテーションによる人材交流、情報システムの統合によるリアルタイムでのデータ共有が効果的です。部門の壁を越えたプロジェクトチームの結成や成功体験の共有も連携強化に役立ちます。
業務プロセスの共有と情報の流通
業務フローを文書化し、各工程の責任部署や連携ポイントを明確にすることで、効率的な生産体制が構築できます。情報共有のためのプラットフォームを整備し、必要な情報に誰でもアクセスできる環境を作りましょう。
部門間の引き継ぎポイントでは、標準化されたフォーマットやチェックリストを活用することで、情報の欠落や誤解を防止できます。
企業全体での改善施策の推進
効率化には、トップマネジメントの強いコミットメントと全社的な推進体制が必要です。全社横断的な改善推進チームの設置や定期的な成果発表会の開催、改善活動の成果を適切に評価・報酬に反映する仕組みにより、継続的な改善文化が醸成されます。
改善活動の進捗を定量的に測定し、PDCAサイクルを回すことで、着実な効果創出が可能になります。
製造業におけるDXの推進
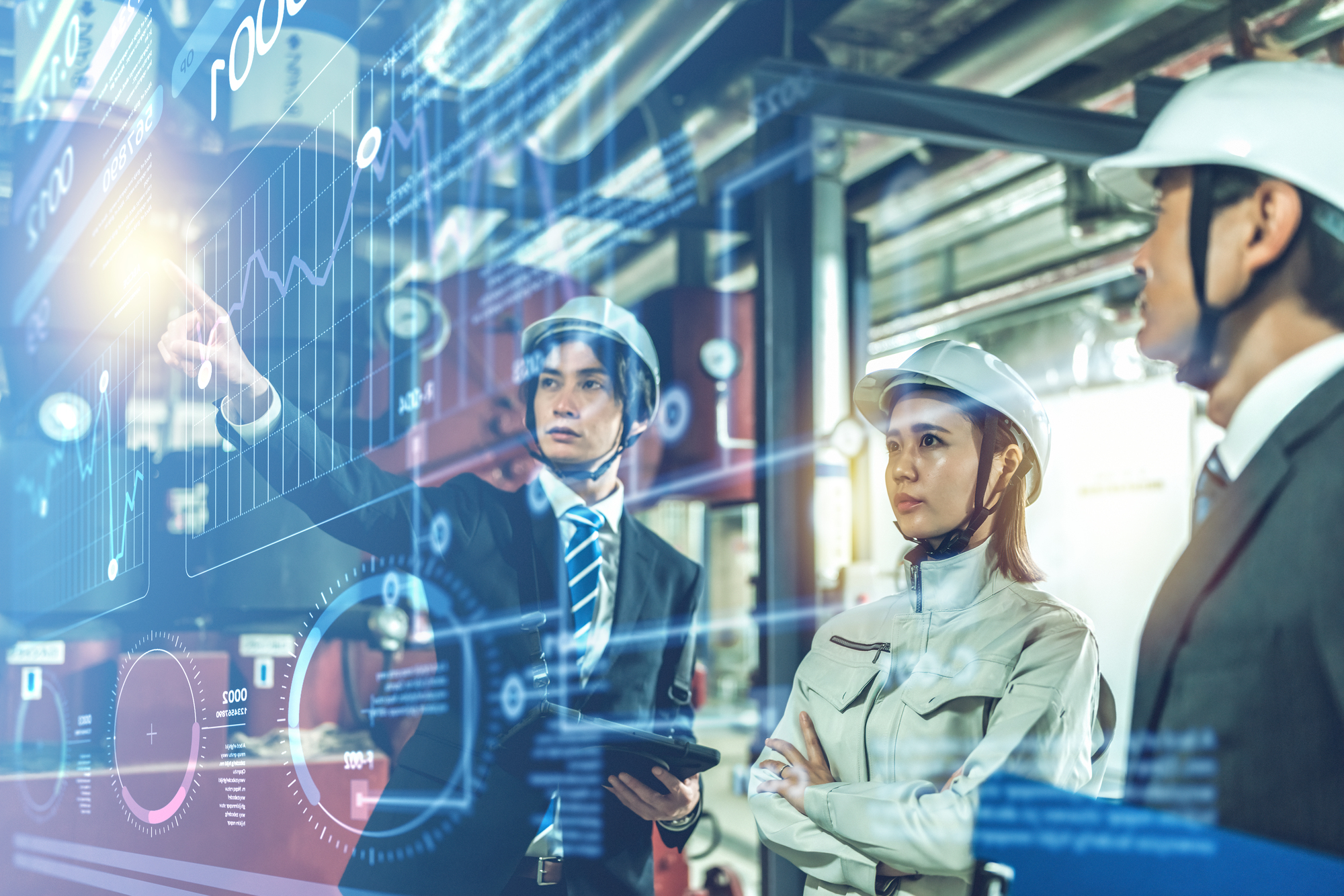
デジタル技術を活用した業務の改革
製造業のDXは、既存の業務プロセスをデジタル技術で効率化するだけでなく、ビジネスモデル自体の変革も目指します。センサー技術やIoTを活用して設備の稼働状況をリアルタイムで収集・分析し、生産計画の最適化や予防保全を実現するスマートファクトリー化が進んでいます。
AR(拡張現実)やVR(仮想現実)を活用した作業支援や教育訓練も導入されています。技術導入の際は、ビジネス課題の解決や顧客価値の向上にどう貢献するかを明確にすることが重要です。
クラウド技術を用いたデータ管理の効率化
クラウド技術を活用すれば設計データ、生産実績、品質情報などを統合的に管理でき、部門間の連携強化と意思決定の迅速化が図れます。
初期投資を抑えながら必要に応じて機能を拡張できる柔軟性も魅力で、場所を選ばずに情報にアクセスできるため、リモートワークとの親和性も高いです。セキュリティ面での懸念は適切な対策と運用ルールの整備で解決できます。
AI・機械学習による業務改善の可能性
AIや機械学習技術は、過去の生産データ分析による最適生産条件の導出、画像認識による高速・高精度な外観検査、需要予測による生産計画精度向上と在庫適正化、製造設備の異常検知や予防保全など、様々な場面で活用されています。
AIの導入に際しては、特定のユースケースを絞り込み、成功体験を積み重ねていくアプローチが有効です。
まとめ
製造業における作業効率向上は、競争力維持と持続的成長のために不可欠な取り組みです。効率化のポイントは、現状の正確な把握と課題の明確化、適切なツールや技術の選定、そして全社一丸となった継続的な改善活動です。現場の声を活かし、小さな成功体験を積み重ねていくアプローチが効果的です。
デジタル技術の進化は製造業に大きな変革をもたらしていますが、技術導入の目的を明確にし、人と技術の最適な組み合わせを追求することが重要です。効率化と品質向上の両立、そして働きやすい職場環境の実現を目指して、継続的な改善に取り組みましょう。